Electronics Manufacturing: Component-Level Traceability
Implementing WMS and MES integration to track individual electronic components from receiving through assembly, enabling rapid identification of affected products when supplier quality issues arise and meeting international electronics traceability standards.
Table of Contents
Toggle1. Industry Context & Customer Profile
Industry Segment: Electronics Manufacturing
The electronics manufacturing industry in Vietnam has grown substantially over the past decade, evolving from simple assembly operations to advanced production of sophisticated components and finished products. Local manufacturers now produce everything from consumer electronics to industrial control systems, with many serving as critical suppliers in global supply chains for major international brands.
Typical Customer
Medium to large electronics manufacturers with 200-1,500 employees, operating multiple production lines assembling printed circuit boards (PCBs), electronic modules, or complete devices. These companies typically process thousands of individual component types daily, manage complex bills of materials (BOMs), and face increasing quality and compliance requirements from their customers.
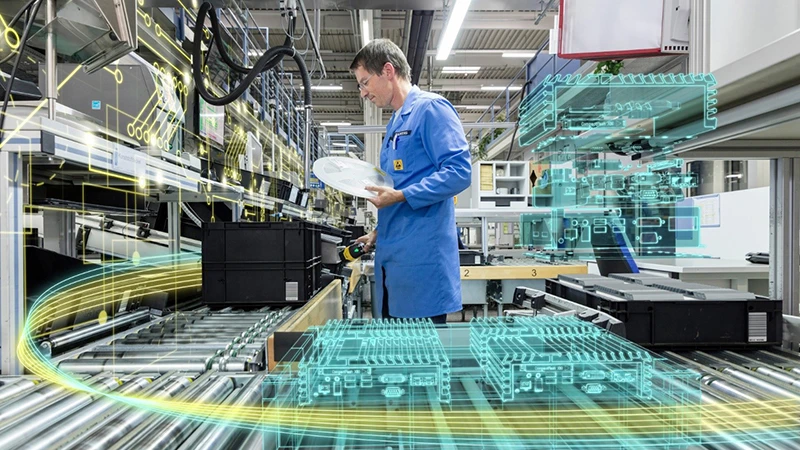
Current Operational Environment
Most electronics manufacturers in Vietnam currently employ limited traceability systems that track only at the lot or batch level. These existing systems typically include:
- Basic inventory management that records receiving dates and supplier information
- Batch-level tracking where components from the same delivery are assigned a common code
- Manual recording of which component batches were used in which production runs
- Paper-based or basic digital documentation systems
- Limited ability to trace beyond final assembly to component origins
One production manager at a contract electronics manufacturer described their traceability system as “adequate for yesterday’s requirements but increasingly insufficient for today’s customer demands.”
2. Critical Pain Points & Challenges
Operational Inefficiencies
Limited component traceability creates significant operational challenges:
- Component recall situations require extensive manual investigation
- Quality issues take days or weeks to trace back to specific component batches
- Quarantine decisions often affect more inventory than necessary
- Material handlers spend excessive time locating and verifying components
- Production delays occur due to component verification procedures
- Inventory accuracy suffers without individual component tracking
A quality director at an electronics manufacturer producing automotive components noted, “When a supplier notifies us of a potential quality issue, we often have to quarantine and inspect weeks of production because we can’t precisely identify which assemblies contain the affected components.”
Compliance & Quality Concerns
Electronics manufacturers face growing compliance and quality requirements:
- Major customers increasingly require component-level traceability
- Automotive electronics must meet IATF 16949 traceability standards
- Medical device electronics require FDA compliance for component tracking
- Aerospace and defense contracts demand complete supply chain visibility
- RoHS, REACH, and other environmental regulations require material documentation
- Counterfeit component prevention requires verification of component origins
These requirements continue to intensify as electronics become more integrated into safety-critical applications. One Vietnam-based electronics manufacturer lost a major contract worth $5 million annually because they couldn’t meet the customer’s traceability requirements.
Cost Pressures
Inadequate traceability systems create substantial financial impacts:
- When quality issues arise, manufacturers often must scrap or rework entire batches
- Limited recall scope leads to excessive replacement costs
- Quality investigation labor costs increase with manual traceability
- Excessive safety stock is maintained to compensate for traceability limitations
- Customer chargebacks occur when defective products cannot be caught before shipping
- Premium freight costs arise when last-minute replacements are needed
A finance director at one electronics manufacturer calculated that limited traceability cost their company approximately 3-4% of annual revenue through scrap, rework, and customer penalties.
Competitive Disadvantages
As global electronics manufacturing becomes more advanced, companies with limited traceability capabilities face growing competitive disadvantages:
- Inability to win contracts with customers requiring advanced traceability
- Higher operating costs reducing price competitiveness
- Extended time-to-resolution for quality issues damaging customer relationships
- Difficulty achieving higher-tier supplier status with multinational customers
- Challenges achieving required quality certifications
- Limited ability to protect brand reputation through rapid, targeted recalls
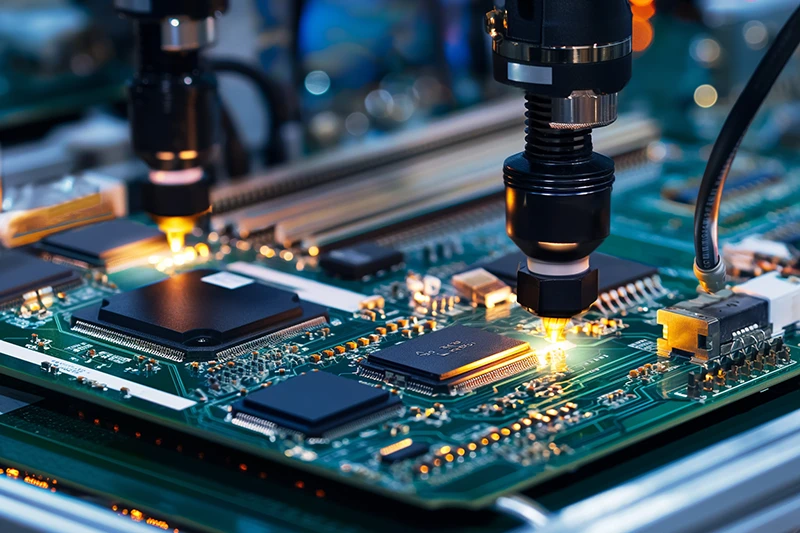
3. DxFactory Solution Overview
Primary DxFactory Components
The DxFactory Component-Level Traceability solution integrates two core systems:
- Warehouse Management System (WMS) – Manages component receiving, storage, and movement with individual tracking
- Manufacturing Execution System (MES) – Controls production processes and records component usage in each assembly
Key Functionalities
The integrated solution provides comprehensive traceability capabilities:
- Component Serialization – Individual tracking of key components through unique identifiers
- Digital Genealogy – Complete record of which components are used in each assembly
- Supplier Integration – Electronic receipt of component data from suppliers
- Automated Verification – Barcode/RFID scanning to confirm correct component usage
- Real-time Tracking – Current location and status of all components in inventory and production
- Bi-directional Traceability – Ability to track forward (which products contain specific components) and backward (which components are in a specific product)
- Rapid Recall Management – Instant identification of affected products when component issues arise
- Compliance Documentation – Automated generation of traceability reports for customers and regulators
Integration Approach
The DxFactory solution integrates with existing manufacturing environments through:
- Connection with existing ERP and inventory systems
- Integration with testing and quality systems
- Compatibility with barcode, RFID, and other identification technologies
- Data exchange with supplier portals and customer systems
- Mobile applications for warehouse and production staff
Technical Requirements
Implementation requires:
- Barcode/RFID infrastructure for component identification
- Network connectivity in warehouse and production areas
- Tablets or workstations at key points in the production process
- Server infrastructure (on-premises or cloud-based)
- Integration middleware for connecting with existing systems
4. Implementation Roadmap
Phase 1: Assessment & Planning (3-4 weeks)
- Evaluation of current traceability capabilities and gaps
- Identification of critical components requiring individual tracking
- Mapping of material flow from receiving through production
- Analysis of customer and regulatory traceability requirements
- Data standardization planning
- Design of component identification methodology
- ROI analysis and project planning
Phase 2: Deployment & Configuration (8-12 weeks)
- Installation and configuration of WMS and MES systems
- Setup of component identification methods (barcode/RFID)
- Configuration of tracking points throughout material flow
- Development of traceability reporting templates
- Integration with existing manufacturing systems
- Data migration from legacy systems
- Configuration of alerts and exception management
Phase 3: Training & Adoption (4-6 weeks)
- Training of warehouse personnel on component receiving and tracking
- Production staff training on component verification procedures
- Quality and compliance team training on traceability reporting
- Pilot implementation on selected production line
- Parallel operation with existing systems for validation
- Process refinement based on initial feedback
- Development of standard operating procedures
Phase 4: Optimization & Expansion (Ongoing)
- Performance review after first month of operation
- Expansion to additional production lines
- Implementation of advanced analytics for component performance
- Supplier portal integration for upstream traceability
- Addition of environmental compliance tracking
- Integration with customer systems for downstream visibility
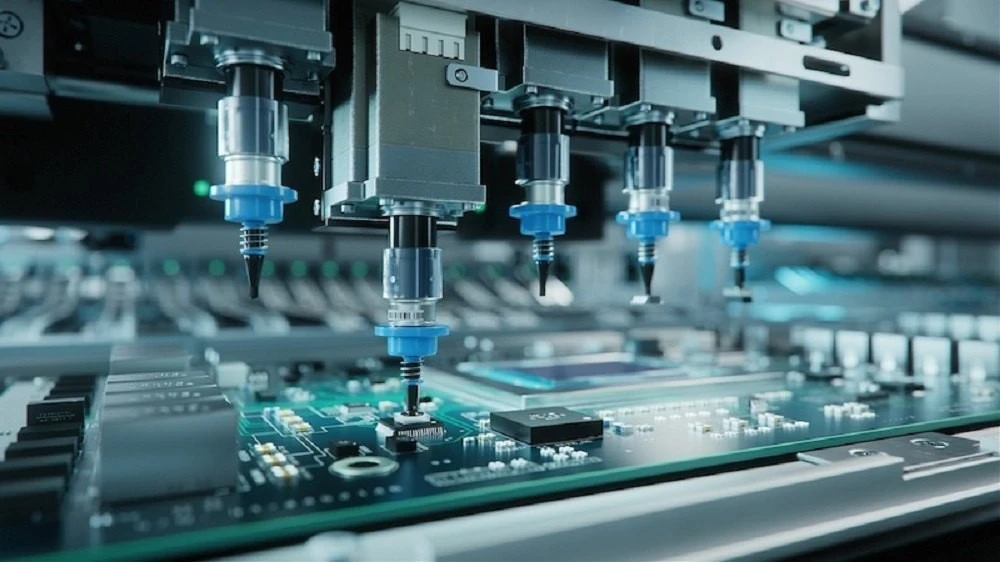
5. Value Delivery & ROI Analysis
Immediate Benefits
Within the first three months of implementation, manufacturers typically experience:
- 90% reduction in time required to identify affected products during component recalls
- 100% accuracy in component verification during assembly
- 60-70% reduction in quality investigation time
- 30% improvement in inventory accuracy
- Complete compliance with customer traceability requirements
A production supervisor at an early adopter commented, “What used to take days of searching through records now takes minutes with a few clicks. When a supplier notified us of a potential issue, we identified exactly which 47 assemblies out of thousands contained the suspect components.”
Operational Improvements
Measured improvements after 6-12 months include:
- 15-20% reduction in component-related defects through better supplier accountability
- 25-30% decrease in time spent on component kitting and verification
- 40-50% reduction in scrap and rework costs through targeted quality actions
- 10-15% improvement in production throughput
- 20-25% reduction in safety stock requirements
Financial Impact
A typical medium-sized electronics manufacturer can expect:
- Return on investment within 10-14 months
- Reduction in quality costs valued at $150,000-$300,000 annually
- Inventory carrying cost savings of $100,000-$200,000 annually
- Labor efficiency improvements valued at $75,000-$150,000 annually
- Reduced risk of costly field failures and recalls (average recall cost: $500,000+)
Competitive Advantage
Manufacturers implementing the DxFactory component traceability solution gain significant market advantages:
- Qualification for high-value contracts requiring advanced traceability
- Ability to serve quality-sensitive market segments (automotive, medical, aerospace)
- Enhanced ability to prove compliance with environmental regulations
- Improved customer confidence through demonstration of quality controls
- Data-driven supplier management for continuous improvement
The implementation of component-level traceability represents a fundamental shift in electronics manufacturing quality management. Beyond merely meeting customer requirements, this capability transforms how manufacturers manage risk, quality, and compliance. As electronics continue to become more integrated into critical systems across industries, the ability to track components from receiving dock to final product will increasingly separate market leaders from companies struggling to compete in a global marketplace.
Related Articles: