Adopt Automation in Manufacturing: How-To, Use Cases & Predictions
Automation in manufacturing refers to the use of advanced technologies and machinery to streamline production processes. It minimizes human intervention by incorporating systems like robotics, artificial intelligence, and IoT-enabled devices. Over the years, automation has transformed the manufacturing sector, shifting it from labor-intensive methods to highly efficient, technology-driven operations. As a result, businesses are increasingly adopting these solutions to stay competitive in a fast-changing market.
This rise in automation stems from the growing demand for faster production, consistent quality, and cost efficiency. Therefore, for modern manufacturers, understanding and embracing automation is not just advantageous but essential. It provides opportunities to optimize operations, meet evolving customer demands, and, importantly, drive innovation across industries.
Table of Contents
Toggle3 Types of Automation in Manufacturing
Automation in manufacturing is categorized based on its functionality and adaptability to production needs. Understanding the differences between fixed, programmable, and flexible automation is key to choosing the right solutions for specific operational goals.
Fixed Automation
Fixed automation is designed for high-volume production with minimal variability. It relies on predefined processes and equipment that are optimized for specific tasks. Common examples include assembly lines in automotive manufacturing and material handling systems like conveyor belts in warehouses.
Assembly lines are a classic example of fixed automation. They use a series of machines and tools arranged in a sequence to produce standardized products efficiently. For instance, in automobile production, each station on the line performs a specific task, such as welding or painting. Once set up, these systems can operate continuously, delivering consistent output at a high speed.
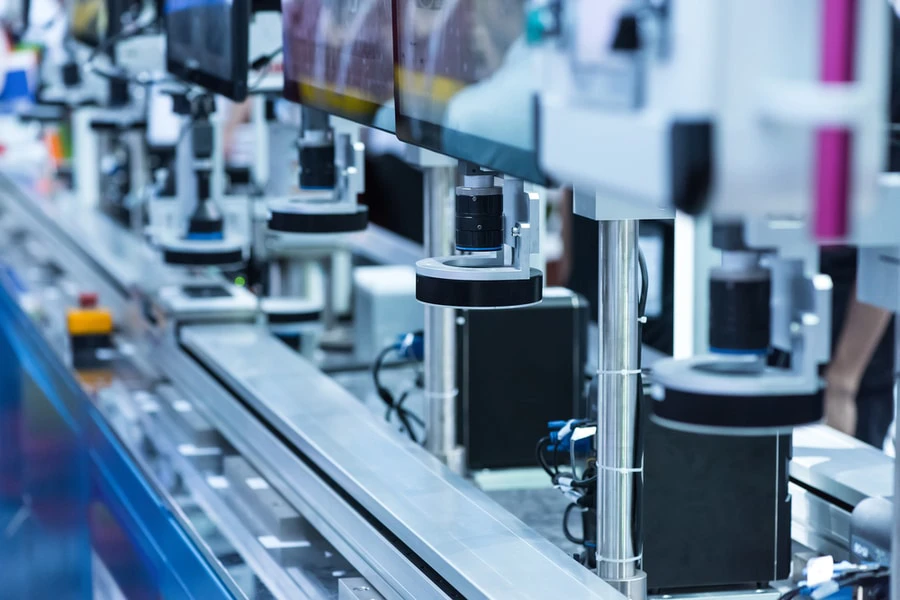
Material handling systems, on the other hand, streamline the movement of goods within factories or warehouses. These systems include conveyors, automated guided vehicles (AGVs), and palletizers, which help reduce manual labor and improve efficiency. While fixed automation offers speed and reliability, it is less adaptable to changes in product design or production requirements.
Programmable Automation
Programmable automation is more versatile, allowing manufacturers to reconfigure processes for different tasks or products. This adaptability makes it ideal for producing batches of goods with variations. Examples include CNC (Computer Numerical Control) machines and robotics for customization.
CNC machines are a cornerstone of programmable automation. These systems are used in industries like aerospace and furniture manufacturing, where precision is critical. Operators can program CNC machines to perform tasks such as cutting, drilling, or milling specific shapes and dimensions. If product designs change, the machines can be reprogrammed, making them an excellent choice for batch production.
Robotics in programmable automation takes this adaptability further. For example, robotic arms equipped with sensors can handle tasks like welding, assembling, or painting. In electronics manufacturing, robots often assemble circuit boards with precision. Their programming allows them to adapt to different configurations, ensuring consistent quality even in complex tasks.
Flexible Automation
Flexible automation builds on the principles of programmable systems, offering even greater adaptability for dynamic production environments. This type is particularly suited for manufacturing facilities that handle multiple product variations or smaller batch sizes. Examples include multi-purpose robots and smart systems.
Multi-purpose robots are highly adaptable machines that can switch between tasks with minimal downtime. For instance, a robot in a factory might handle packaging one day and quality inspection the next, simply by updating its programming. This flexibility reduces the need for multiple specialized machines, saving both time and costs.
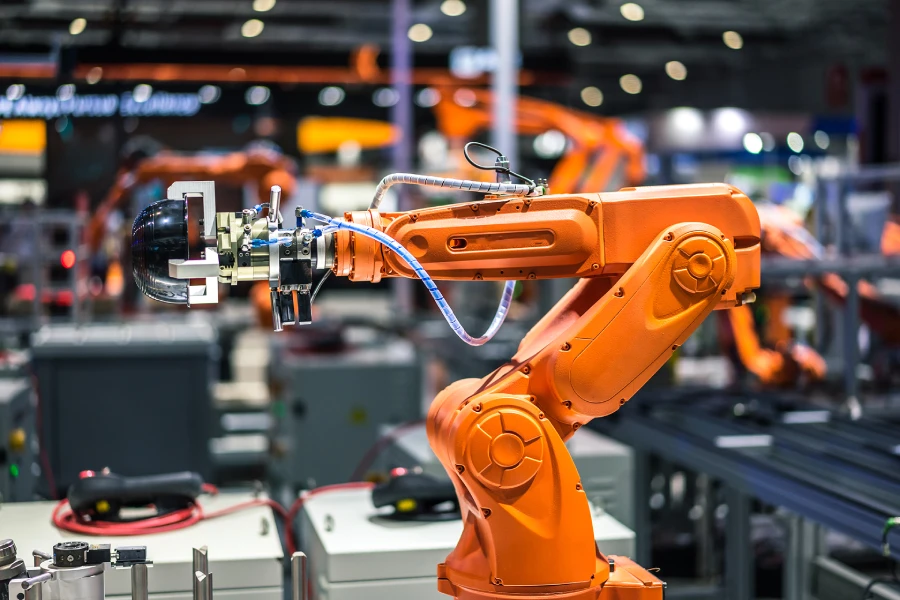
Smart systems, driven by technologies like artificial intelligence and IoT, take automation to another level. These systems can self-adjust based on real-time data. For example, in a smart factory, IoT-enabled sensors can monitor production conditions and automatically optimize machine settings. This level of automation improves efficiency and responsiveness to changing demands.
While fixed automation excels in high-volume production, programmable and flexible automation are better suited for versatility and adaptability. Selecting the right type depends on production goals, product complexity, and desired output.
Key Technologies in Manufacturing Automation
Technology is breathing new life into manufacturing, making it faster, smarter, and way more precise. The tools driving these changes aren’t just fancy gadgets—they’re shaping how factories run, products are made, and workers get their jobs done. Let’s break down some of the big players making waves in automation today.
Robotics and Cobots (Collaborative Robots)
Robots have been the backbone of factory automation for years. They’re perfect for heavy lifting, welding, and other tasks that demand unwavering accuracy and speed. But here’s where it gets exciting: cobots, or collaborative robots, are showing up more and more on shop floors. These machines are designed to work side by side with people without turning the workplace into a safety hazard.
Cobots are super handy for repetitive, boring jobs that no one really enjoys, like packaging or assembly. They don’t just follow commands blindly—they’re packed with sensors that let them adjust on the fly, so they’re much less likely to mess up or put workers in danger. In smaller factories, cobots often act like helpful coworkers, freeing up humans to handle the more brainy, creative stuff.
Industrial Internet of Things (IIoT)
Think of the IIoT as the nervous system of a smart factory. It connects machines, sensors, and systems so they can talk to each other and share data. The best part? It doesn’t just make everything more efficient—it lets you keep tabs on what’s happening in real-time, whether it’s spotting a hiccup on the production line or predicting when a machine needs a tune-up.
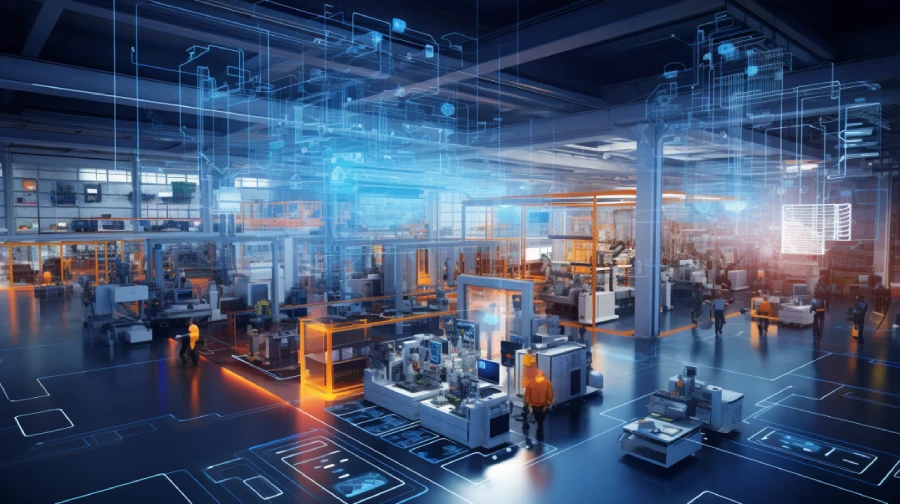
A great example is sensor-packed equipment that can ping you the moment it detects something’s off, like overheating or misaligned parts. You get a heads-up before things spiral out of control, which saves money and headaches. With IIoT, factories run smoother, downtime is slashed, and waste takes a nosedive.
Artificial Intelligence and Machine Learning
AI and machine learning are like the brains behind today’s high-tech factories. They don’t just crunch numbers; they make smart calls based on patterns and predictions. These systems are pros at juggling tasks like tweaking production schedules, managing inventory, and making sure products are consistent across the board.
Here’s an example: AI can monitor a production line and automatically tweak settings to keep quality at its peak. If something starts veering off course, it adjusts without needing anyone to hit a button. And the coolest part? Machine learning systems get better the more they’re used. They learn from past mistakes and adapt to new challenges, so they’re always on their A-game.
Vision Systems for Quality Control
Cameras in factories aren’t just for security anymore—they’re stepping up as the watchdogs of quality. These vision systems scan products at lightning speed, flagging anything that doesn’t meet the standard.
Take electronics manufacturing, where these systems are champs at spotting misplaced components or tiny defects on circuit boards. They work faster and more accurately than human eyes, which means fewer errors and less waste. Plus, they’re always working, so nothing slips through the cracks.
Autonomous Vehicles in Manufacturing
Self-driving vehicles aren’t just for futuristic cities—they’re changing how materials move around in factories too. Automated guided vehicles (AGVs) and autonomous mobile robots (AMRs) handle tasks like shuttling raw materials to production lines or delivering finished goods to storage.
Unlike traditional systems that follow set paths, AMRs can navigate on the go. Say there’s an obstacle in their way; they’ll figure out a new route without skipping a beat. This flexibility keeps operations humming along without unnecessary delays.
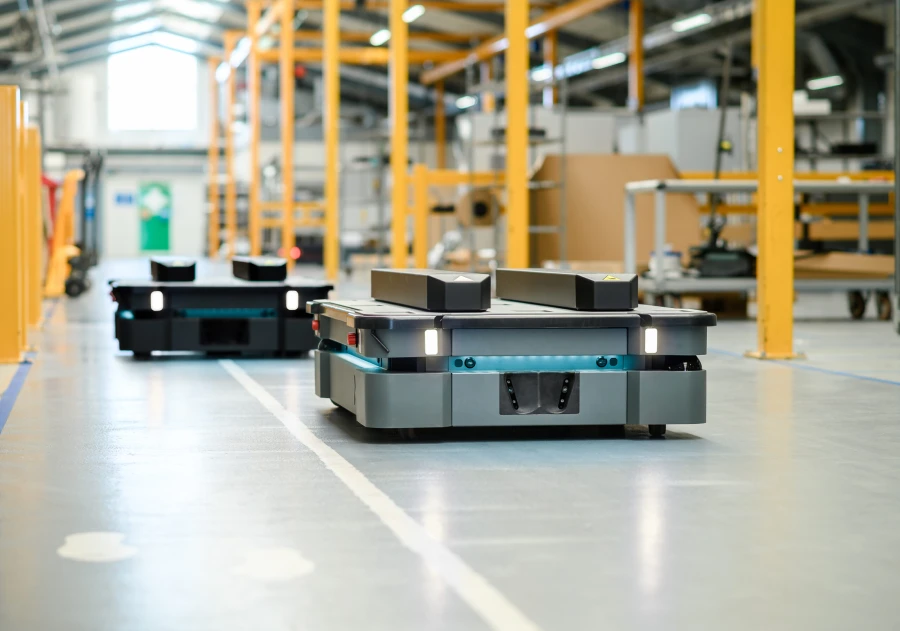
Cloud and Edge Computing in Manufacturing
Big data needs big computing power, and that’s where cloud and edge computing come into play. Cloud computing lets factories analyze data from anywhere, while edge computing handles things on-site for quicker response times.
In a smart factory, edge computing can crunch numbers right at the source—like adjusting machine settings the instant something looks off. Meanwhile, cloud computing helps you see the bigger picture, letting teams collaborate and plan more effectively. Together, they’re turning mountains of data into actionable insights, making operations sharper and more responsive.
5 Main Benefits of Automation in Manufacturing
Improved Productivity and Efficiency
Automation takes the grunt work out of the equation. Machines don’t need breaks, don’t get tired, and don’t lose focus. They can work around the clock without missing a beat, which means production speeds up and overall output increases. Instead of employees spending time on repetitive tasks, they can focus on the creative and more complex aspects of production. It’s like turning your factory into a well-oiled machine where everything runs smoothly, even when you’re not looking.
For instance, robots on an assembly line can handle repetitive tasks at a pace humans can’t keep up with, like tightening bolts or sorting parts. The result? The entire production process accelerates, reducing bottlenecks and delivering more products in less time. This not only boosts productivity but also makes the whole system more efficient.
Enhanced Quality and Accuracy
The thing with humans? We can make mistakes. But machines, they do exactly what you tell them to, every single time. Automation’s biggest selling point is the way it locks in consistency. Whether it’s producing a batch of identical parts or assembling a product, the outcome is far more predictable and precise.
Take quality control, for example. With automated systems that check for defects or measure parts, the chances of human error are dramatically reduced. These systems can inspect every inch of a product, looking for flaws that would be impossible for a person to catch. The result is a product that meets the highest standards without the need for extra manual checks. What’s better? As the system runs, it learns and improves, so the quality keeps getting better over time.
Cost Savings in the Long Term
On the surface, automation can seem like a big upfront investment. But when you look at it from a longer-term perspective, the savings start to add up. With robots, machines, and automated systems handling production, you reduce the need for manual labor. This cuts down on labor costs, training, and turnover.
Additionally, with automation, mistakes are fewer, waste is minimized, and downtime is reduced. Machines can work continuously, meaning you’re maximizing output without worrying about breaks, sick days, or overtime pay. Over time, those savings make a massive difference to your bottom line. It’s like buying a quality tool that keeps paying off year after year.
Better Workplace Safety and Reduced Injuries
Factories can be dangerous places, with heavy machinery and hazardous materials posing risks to workers. Automation, however, significantly cuts down on these hazards. Dangerous tasks like lifting heavy objects, working with sharp tools, or handling toxic substances can be taken over by machines or robots, leaving human workers to do the jobs that are safer and more creative.
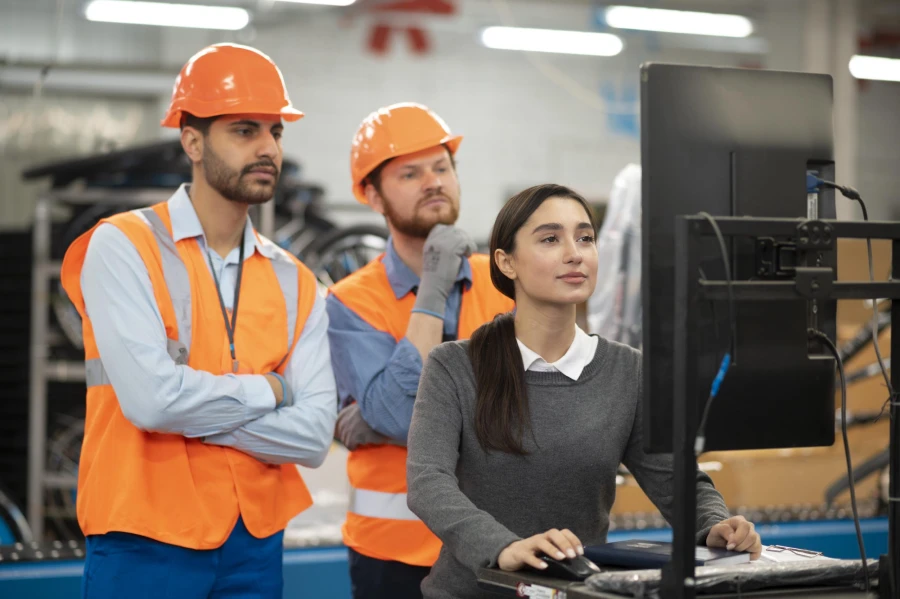
This isn’t just about keeping your team safe—it also means fewer workers need to take time off due to injuries. Plus, fewer accidents mean fewer insurance claims, which translates to lower operational costs. In the long run, a safer environment is not just better for employees, but it’s also better for the business’s financial health.
Scalability and Adaptability to Market Demands
The manufacturing industry doesn’t stay the same for long. Customer demands change, new products emerge, and market trends shift. That’s where automation really shines. Automated systems can be adjusted quickly to meet these new demands, whether it’s switching out products, adjusting production speed, or scaling up to meet sudden surges in orders.
For example, in a clothing factory, switching from making one type of garment to another can be a hassle without automation. But with the right automated equipment, you can reprogram the systems and change the setup in less time than it would take a team of people to manually retool everything. This kind of flexibility is what helps businesses stay competitive and respond to market changes without missing a beat.
5 Challenges of Implementing Automation
High Initial Investment Costs
Let’s face it, automation is not cheap. At the outset, you’re looking at significant investments in hardware, software, and installation. High-tech robots, specialized machines, and custom software solutions can all carry hefty price tags, which might be tough to swallow for businesses, especially smaller ones. These initial expenses can be hard to justify when the return on investment (ROI) isn’t immediately clear.
But here’s the kicker: while the upfront costs can feel overwhelming, the long-term savings often make up for it. Automation can improve productivity, reduce errors, and cut labor costs, all of which contribute to a better bottom line over time. Still, figuring out how to cover those first expenses can be a major obstacle.
Integration Complexity with Legacy Systems
Another tough nut to crack is getting automation to play nice with the old systems you’ve been using for years. Legacy systems, which are often outdated and not designed to communicate with modern technology, can cause major headaches during the integration process.
Imagine trying to connect a brand-new robot to a machine that was installed back in the 90s. It doesn’t always go smoothly, and the cost of upgrading or replacing older equipment can quickly add up. Plus, employees will need time to adapt to the new technology, which can lead to downtime and temporary loss in productivity. The complexity of making everything work together smoothly can be a real challenge, especially if the system wasn’t designed with integration in mind.
Skill Gaps and Workforce Training Needs
Let’s be honest: automation isn’t something everyone can jump into without a little training. The technology behind automation can be complex, and your current workforce might not have the skills needed to operate and maintain these new systems.
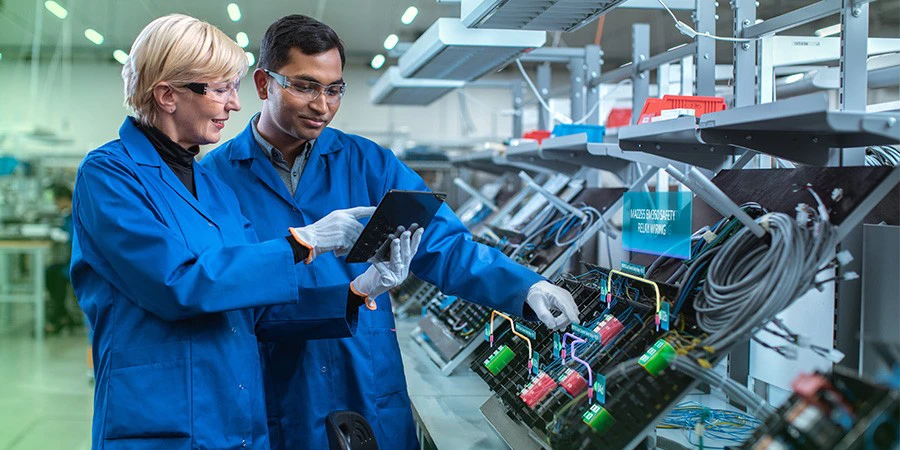
Whether it’s programming robots, troubleshooting automation software, or using advanced control systems, there’s a lot to learn. This means that businesses will need to invest in training programs or hire new talent with the right expertise. Both options come with their own set of challenges—training takes time and money, while hiring specialists may be difficult due to the growing demand for skilled automation workers.
Cybersecurity Risks in Automated Systems
Automation introduces a whole new level of exposure to cybersecurity threats. As systems become more connected, whether through the cloud or the Industrial Internet of Things (IIoT), they become vulnerable to cyberattacks. A breach in the system could lead to everything from production shutdowns to theft of sensitive company data.
Securing automated systems requires businesses to invest in strong cybersecurity measures, including firewalls, encryption, and constant monitoring. And, as with most areas of tech, the landscape of threats is always shifting, so staying ahead of the curve can be a daunting task. Companies may find it hard to keep up with these new risks without specialized security professionals on their teams.
Resistance to Change Within Organizations
No matter how beneficial automation can be, there’s always resistance to change. Employees, especially those who have been with the company for years, may feel threatened by the introduction of robots and automation. They might worry about losing their jobs or fear that the new systems will make their roles redundant.
Overcoming this resistance requires clear communication and a focus on retraining staff. Showing employees how automation can take over the more dangerous or monotonous tasks, allowing them to focus on higher-value work, is key to getting buy-in. The transition might take time, but the result can be a smoother shift towards automation with happier employees.
Common Use Cases of Automation in Manufacturing
Automotive Assembly and Testing
In the automotive industry, assembly lines have long been synonymous with precision and speed. But automation has taken these qualities to new heights. Robotic arms, for instance, are now commonly used to handle the heavy lifting—literally. They take care of tasks like welding, screwing in bolts, and assembling intricate parts, all while ensuring consistency and reducing the chance of errors.
Testing is another area where automation shines. Automated systems can quickly run diagnostics on every single vehicle, checking everything from engine performance to safety features, and alerting workers if something’s off. This not only speeds up production but also ensures that every car meets high-quality standards before it rolls off the line.
Electronics Manufacturing and Quality Control
When it comes to electronics, precision is everything. A small mistake can result in malfunctioning devices or, worse, product recalls. Here, automation systems are key players. Automated assembly lines can assemble tiny components, like circuit boards or chips, with incredible speed and accuracy. This minimizes human error and ensures that each component is placed correctly.
On top of that, robots are also essential for quality control. They’re able to conduct thorough inspections, scanning for defects that would be almost impossible to spot manually. Whether it’s a tiny crack in a phone screen or a misplaced solder joint, automated systems can catch these issues early on, preventing costly mistakes later.
Food and Beverage Production Lines
Food and beverage production lines are also benefiting from automation, particularly when it comes to consistency and hygiene. Automated machines can handle everything from mixing ingredients to filling and sealing containers. These systems operate at a much faster rate than human workers, ensuring that large volumes of product are produced without sacrificing quality.
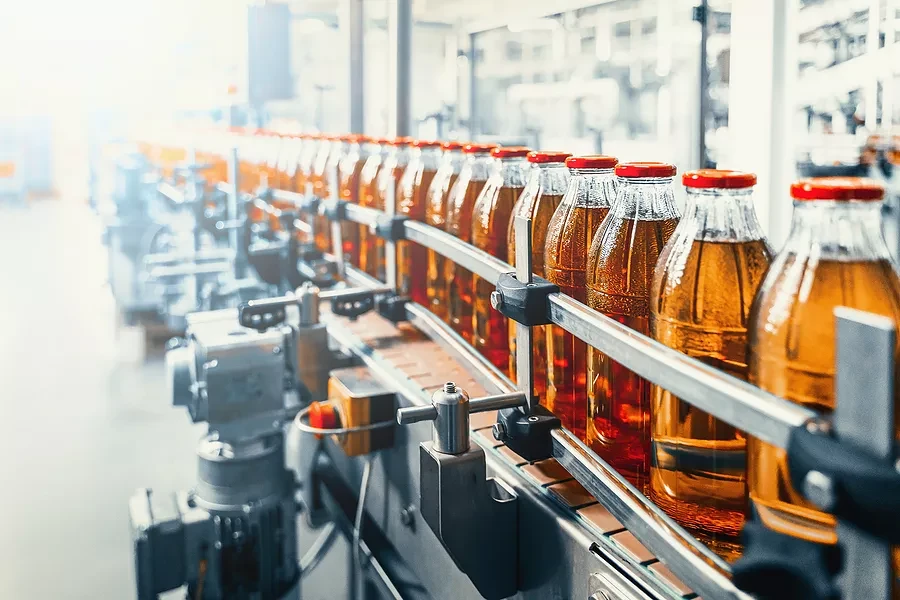
Take a bottling line, for example. Machines can fill thousands of bottles an hour, accurately measuring the exact amount of liquid for each. Not only does this boost efficiency, but it also reduces the risk of contamination, as robots can work in sterile environments, unlike humans. The end result? More product, fewer errors, and better consistency.
Pharmaceutical Packaging and Inspection
In the pharmaceutical industry, the stakes are incredibly high. When you’re dealing with life-saving medications, there’s no room for mistakes. Automation helps ensure that pharmaceutical packaging and inspection processes are carried out with extreme care and efficiency. Automated systems handle everything from labeling to packaging, all while maintaining compliance with strict regulatory standards.
Robotic systems also assist in inspection, checking for issues like missing labels or incorrect packaging. This is particularly important for ensuring that the right medication reaches the right place, minimizing the risk of errors that could affect patient safety. With automation, manufacturers can achieve faster turnaround times without sacrificing quality or safety.
Customization in Small Batch Manufacturing
When it comes to small-batch manufacturing, automation provides manufacturers with a level of flexibility that’s hard to beat. Whether it’s crafting custom-made products or adapting to shifting consumer preferences, automated systems are adaptable enough to handle smaller, more specialized production runs.
In industries like furniture or apparel, for example, automation allows for on-demand customization. Machines can quickly adjust to different designs or measurements, ensuring that each item is unique, without slowing down production. This helps businesses stay nimble in a competitive market where customer preferences can change rapidly.
5 Steps to Adopt Automation in Manufacturing
Adopting automation in manufacturing isn’t something you can rush into without a solid plan. It’s more than just adding a robot to your assembly line. The process involves careful thought, smart choices, and ongoing adjustments to make it work for your business. Here’s how to approach it in five clear steps.
1. Assessing Business Needs and Goals
Before you get too excited about shiny new technology, start by looking at what your business really needs.
Ask yourself: What problems are you trying to solve? Are you looking to cut down on labor costs, increase production speed, or improve product quality?
Pinpointing these goals will help you find the best way automation can improve your operations. Take the time to really dig into the specific challenges your company faces. This way, you can focus on automation solutions that hit your exact pain points and align with where you want to take your business.
2. Choosing the Right Automation Technologies
Now that you know what you want to achieve, it’s time to pick the right tech for the job.
There are all kinds of automation solutions out there, from robotic arms to automated inspection systems. The trick is matching the right technology to your needs.
If you’re trying to speed up assembly, a robot might be your best bet. If you need to improve precision in quality control, automated vision systems could do the job.
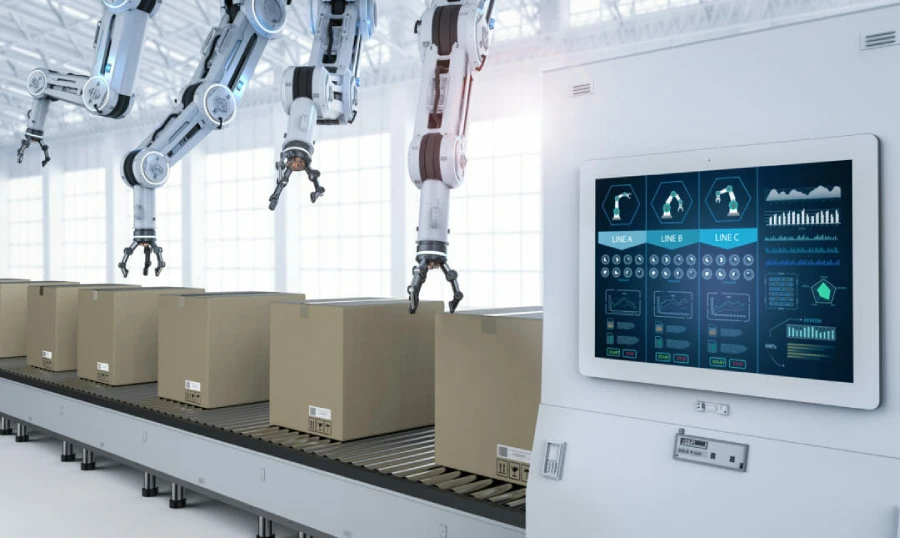
Think about factors like how much space you have, how flexible your production lines need to be, and how much you’re willing to spend. Taking the time to evaluate these details will help you avoid jumping in with technology that might not be the best fit for your needs.
3. Creating a Detailed Implementation Plan
Once you’ve figured out what technology you need, it’s time to set up a clear, step-by-step plan. This should outline how you’re going to roll out automation from start to finish.
Think about what’s involved in setting up the systems, how long it will take, and what resources you’ll need along the way. You’ll also want to factor in any downtime needed to install the systems, as well as how to integrate them with your current operations.
Don’t forget about budgeting—make sure to account for not only the initial costs of purchasing the equipment but also the long-term maintenance and upgrades. Break the plan into phases so that you can manage each part as it comes.
4. Employee Training and Upskilling
Automation doesn’t mean replacing your entire workforce; it’s about helping your team work more efficiently. That’s why it’s so important to invest in training. Your employees will need to learn how to operate, monitor, and maintain the new automated systems.
Some might need additional skills to handle more complex machines, while others could benefit from understanding how automation affects their work and how they can adapt to new roles. Training your team properly helps them feel comfortable with the changes and allows them to see automation as an opportunity, not a threat.
5. Measuring ROI and Continuous Optimization
Once automation is in place, the real work begins. You’ll want to regularly assess how well things are going and whether your investment is paying off.
This means tracking key metrics like production speed, quality control, and even employee satisfaction. Are you hitting your initial goals? If not, what needs adjusting? And just as importantly, automation doesn’t stop after the first phase.
Technology keeps improving, and so should your systems. Keep an eye out for new tools or upgrades that can make your automation work even better.
The Future of Automation in Manufacturing
As automation continues to make its mark in manufacturing, what lies ahead is even more exciting. New technologies and smarter ways of working are pushing boundaries, and it’s clear that the future of manufacturing will look very different from today.
Growth of Smart Factories
Smart factories are the future, where everything is connected, monitored, and adjusted in real-time. Imagine an entire manufacturing plant filled with machines that can communicate with each other, share data, and make decisions based on what’s happening right now.
This is becoming more of a reality as the Internet of Things (IoT) connects machines, sensors, and systems across factories. Smart factories aren’t just about making processes more efficient; they’re about having the flexibility to adapt on the fly and catch issues before they even become problems. The efficiency boost is massive, and it’s only going to grow as more companies embrace this level of connectivity.
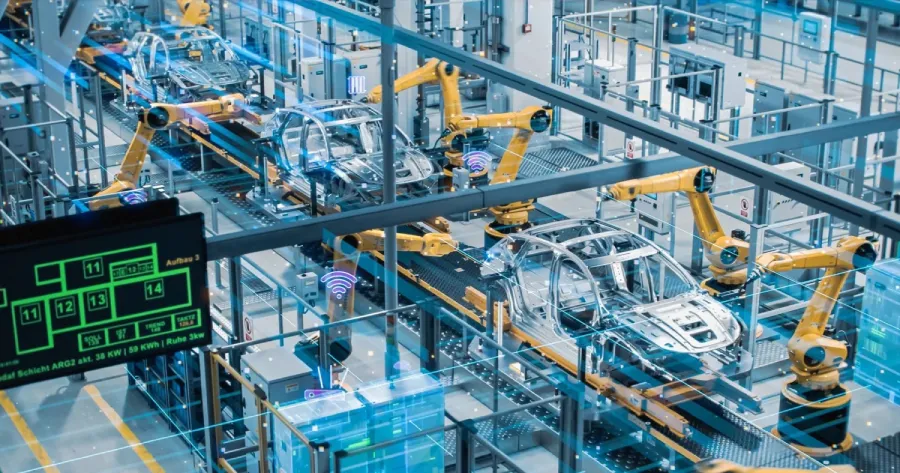
Role of Sustainable and Green Automation
Sustainability is no longer a buzzword—it’s becoming a necessity. As automation continues to evolve, green technologies are being woven into the fabric of manufacturing.
Automated systems now help factories reduce waste, minimize energy usage, and recycle materials more efficiently. Machines can optimize their own processes to use less power, and systems can even adjust based on environmental data to avoid overproduction.
In a world where being environmentally responsible is not just expected but demanded, sustainable automation offers a way for manufacturers to stay ahead of regulations while also cutting costs in the long run.
Integration of Digital Twins and Simulation Models
Digital twins—virtual replicas of physical machines or entire factories—are bringing a whole new level of precision to manufacturing. These digital models can simulate real-world operations, allowing companies to test out processes, predict failures, and tweak systems all without touching the physical equipment.
This simulation technology is especially valuable when designing new systems or improving existing ones. It means fewer mistakes, less downtime, and a much smoother transition to automation. It’s like having a backup plan that’s constantly running, ready to solve problems before they happen.
Advancements in Predictive Maintenance and Analytics
Predictive maintenance is set to change the way manufacturers keep their machines in top shape. With the help of AI, machines can now monitor their own health and predict when they’re likely to break down, so you can fix them before they fail. This cuts down on unexpected downtime and prevents costly repairs.
Coupled with advanced analytics, manufacturers can analyze vast amounts of data to understand trends and improve production. The combination of these technologies means factories will run smarter, not harder, with less downtime and fewer disruptions.
Automation is transforming manufacturing, making it faster, more efficient, and less prone to errors. From streamlining production to improving quality control, it’s clear that automation isn’t just a trend but a necessity. As factories adopt smarter systems, they can keep up with the competition and meet rising demands with ease.
If your business is still hesitant about automation, now’s the time to act. Embracing automation not only cuts costs but also opens doors to innovation and growth. Take the leap now to stay ahead, optimize processes, and give your company the edge it needs in today’s fast-paced market.
Related Articles: