Packaging Industry: Changeover Time Reduction
Implementing MES and CMMS integration to optimize equipment changeovers between different packaging formats/products, digitizing setup procedures with electronic work instructions, tracking changeover performance metrics by team/shift, and identifying opportunities to reduce downtime through SMED principles and preventive maintenance scheduling.
Table of Contents
Toggle1. Industry Context & Customer Profile
Industry Segment: Packaging Industry
The packaging industry in Vietnam has experienced substantial growth in recent years, driven by expanding food processing, pharmaceutical, and consumer goods manufacturing sectors. As consumer preferences evolve and brands seek product differentiation, packaging operations face increasing pressure to handle greater product variety with smaller batch sizes, making changeover efficiency a critical factor in overall productivity and profitability.
Typical Customer
Medium to large packaging companies with 100-500 employees operating multiple packaging lines for food, beverage, pharmaceutical, or consumer goods products. These operations typically run 5-20 packaging lines, managing 30-100 different product formats with changeovers occurring 2-5 times daily per line. Production runs range from high-volume standard products to specialized short-run packaging requiring frequent format changes.
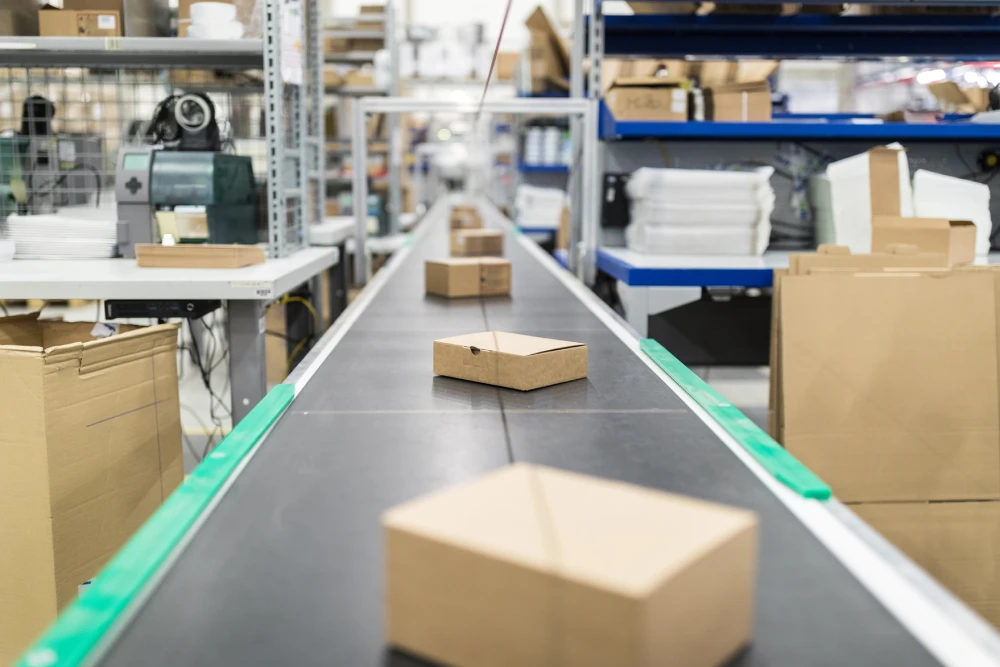
Current Operational Environment
Most packaging operations in Vietnam currently manage changeovers with limited standardization and minimal performance tracking:
- Paper-based setup instructions that vary by operator and shift
- Changeover procedures based primarily on tribal knowledge
- Manual adjustment processes with significant trial and error
- Limited measurement of actual changeover times
- No systematic tracking of changeover performance by product type or team
- Maintenance activities scheduled separately from changeovers
- Minimal application of Single-Minute Exchange of Die (SMED) principles
A production supervisor at a food packaging facility described their situation: “Each changeover feels like starting from scratch. Operators have their own methods, and setup times for the same product changeover can vary by 30-40% depending on who’s working. We waste hours each week producing scrap while dialing in settings after a format change.”
2. Critical Pain Points & Challenges
Operational Inefficiencies
Current changeover approaches create significant operational problems:
- Excessive downtime between production runs (averaging 45-90 minutes per changeover)
- High variability in changeover duration (20-50% variance for identical changes)
- Material waste during restart and adjustment (5-10% of production following changeover)
- Production capacity loss of 15-25% due to changeover inefficiency
- Frequent quality issues immediately following changeovers
- Difficulty planning production schedules due to unpredictable changeover times
- Knowledge gaps when experienced operators are absent
The operations director at a pharmaceutical packaging company explained: “With consumer demand shifting toward smaller, more frequent orders, we’re doing twice as many changeovers as five years ago. Our equipment is capable of higher throughput, but we’re losing nearly 20% of our potential capacity to inefficient changeovers. It’s becoming our biggest production bottleneck.”
Compliance & Quality Concerns
Beyond operational efficiency, packaging manufacturers face growing quality and compliance challenges:
- Strict documentation requirements for pharmaceutical and food packaging changeovers
- Validation requirements for critical settings and parameters
- Traceability of who performed and verified changeover procedures
- Consumer safety concerns requiring thorough cleanout procedures
- Risk of cross-contamination between products
- Quality consistency issues during early production following changeovers
These requirements become especially challenging with regulated products. One quality manager noted: “Every changeover represents a potential point of failure for product quality and safety. We need each step performed consistently every time, with proper verification, regardless of who’s on shift.”
Cost Pressures
The financial impact of inefficient changeovers extends throughout operations:
- Direct labor costs during non-productive changeover time
- Lost production opportunity costs (typically $500-$3,000 per hour)
- Material waste during restart and adjustment phases
- Higher inventory costs to compensate for long production runs
- Premium charges for expedited orders when changeovers take longer than planned
- Additional quality inspection costs following changeovers
A financial analyst at a packaging company calculated: “Each hour of changeover time across our operation costs approximately $1,200 in direct costs and lost opportunity. With over 100 changeovers weekly, even a 15-minute reduction per changeover would save us nearly $400,000 annually.”
Competitive Disadvantages
Manufacturers struggling with changeover efficiency face significant competitive disadvantages:
- Limited flexibility to accommodate short-run orders
- Longer lead times for customer orders
- Higher minimum order quantities to justify changeover costs
- Reduced capacity for new business
- Higher operational costs reducing price competitiveness
- Difficulty meeting just-in-time delivery requirements
3. DxFactory Solution Overview
Primary DxFactory Components
The DxFactory Changeover Optimization solution integrates two complementary systems:
- Manufacturing Execution System (MES) – Core platform managing production scheduling and performance tracking
- Computerized Maintenance Management System (CMMS) – System coordinating equipment maintenance and setup tools
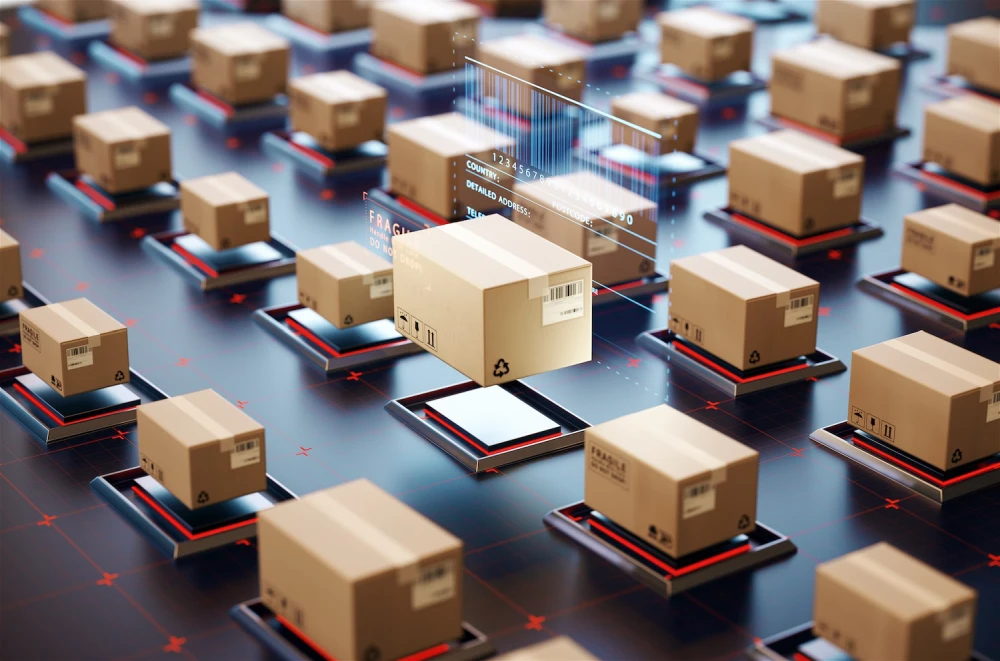
Key Functionalities
The integrated solution provides comprehensive changeover management capabilities:
- Digital Work Instructions – Standardized step-by-step procedures with visual guides
- Changeover Performance Tracking – Real-time monitoring and historical analysis of setup times
- SMED Methodology Implementation – Digital tools supporting internal/external task separation
- Setup Tool Management – Tracking and maintenance of changeover-specific equipment
- Predictive Scheduling – Data-driven forecasting of changeover duration by product type
- Video Recording and Analysis – Capabilities for capturing and reviewing changeover procedures
- Best Practice Sharing – Platform for documenting optimal techniques across shifts
- Maintenance Integration – Coordination of preventive maintenance during planned changeovers
- Training Management – Skills tracking and certification for changeover procedures
- Performance Analytics – Comparative analysis by team, shift, equipment, and product type
Integration Approach
The DxFactory solution integrates with existing manufacturing environments through:
- Connection with production planning and scheduling systems
- Integration with quality management systems
- Digital displays for work instruction delivery
- Mobile applications for operators and supervisors
- Video capture systems for procedure analysis
- Maintenance planning integration
Technical Requirements
Implementation requires:
- Server infrastructure (on-premises or cloud-based)
- Network connectivity throughout production facility
- Digital displays or tablets at packaging lines
- Video recording capabilities at key equipment
- Integration middleware for connecting with existing systems
- Optional IoT sensors for advanced monitoring
4. Implementation Roadmap
Phase 1: Assessment & Planning (3-5 weeks)
- Analysis of current changeover procedures
- Time-motion studies of representative changeovers
- SMED analysis to identify internal/external activities
- Identification of high-impact improvement opportunities
- Development of standardized changeover procedures
- Definition of performance metrics and targets
- Stakeholder alignment and project planning
Phase 2: Deployment & Configuration (6-8 weeks)
- Installation and configuration of MES and CMMS systems
- Development of digital work instructions with visual guides
- Setup of changeover tracking and reporting
- Configuration of maintenance integration
- Implementation of digital displays and mobile applications
- Integration with existing manufacturing systems
- Development of changeover analytics dashboards
Phase 3: Training & Adoption (4-6 weeks)
- Operator training on standardized procedures
- Supervisory training on performance monitoring
- Maintenance staff training on integrated scheduling
- Limited pilot implementation on selected packaging line
- Process refinement based on initial feedback
- Development of standard operating procedures
- Change management and communications program
Phase 4: Optimization & Expansion (Ongoing)
- Performance analysis after first month of operation
- SMED workshops for continuous improvement
- Expansion to additional packaging lines
- Implementation of advanced analytics
- Development of changeover-focused preventive maintenance
- Ongoing procedure optimization based on data
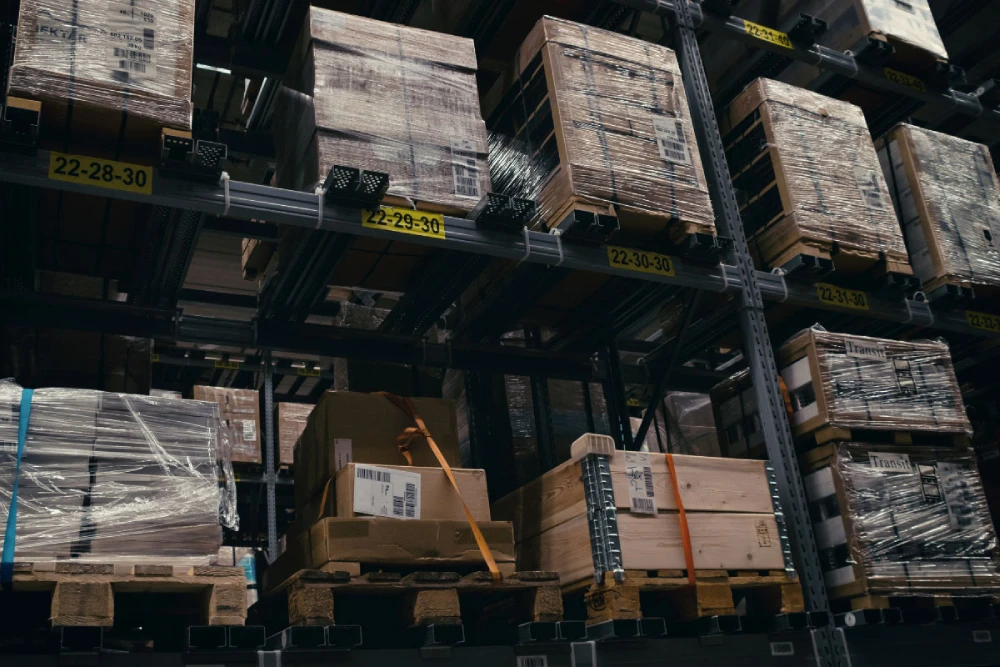
5. Value Delivery & ROI Analysis
Immediate Benefits
Within the first three months of implementation, manufacturers typically experience:
- 20-30% reduction in average changeover time
- 50-60% decrease in changeover time variability
- 15-25% reduction in material waste during restart
- Complete visibility into changeover performance metrics
- 70-80% reduction in quality issues following changeovers
A production manager at an early adopter shared, “The difference was immediate and measurable. Our average changeover went from 68 minutes to 49 minutes within the first month. More importantly, the consistency allowed us to schedule more accurately, essentially giving us back 45 minutes of production capacity per line each day.”
Operational Improvements
Measured improvements after 6-12 months include:
- Total changeover time reduced by 40-50%
- Overall equipment effectiveness (OEE) improved by 8-12%
- Production schedule adherence improved from typical 75% to 90%+
- Setup-related quality defects reduced by 70-80%
- Cross-training effectiveness improved by 40-50%
Financial Impact
A typical medium-sized packaging operation can expect:
- Return on investment within 6-9 months
- Production capacity increase valued at $300,000-$700,000 annually
- Material waste reduction of $50,000-$150,000 annually
- Labor efficiency improvements of $75,000-$200,000 annually
- Quality cost reduction of $40,000-$100,000 annually
Competitive Advantage
Manufacturers implementing the DxFactory changeover optimization solution gain significant competitive advantages:
- Ability to profitably handle smaller batch sizes
- Enhanced flexibility to accommodate rush orders
- Improved responsiveness to changing market demands
- Lower minimum order quantities for customers
- Data-driven operations enabling continuous improvement
- Better utilization of existing equipment
The implementation of integrated changeover management represents a transformative capability for packaging operations. By combining standardized procedures, performance measurement, and continuous improvement methodologies, manufacturers can dramatically reduce one of their largest sources of lost productivity. As market dynamics continue to favor greater product variety and smaller batch sizes, this capability will increasingly separate industry leaders from those struggling with the fundamental economics of high-mix packaging production.
Related Articles: