Pharmaceutical: Electronic Batch Record Management
Deploying integrated ERP and QMS to maintain complete electronic batch records, ensuring GMP compliance, enabling paperless validation processes, and providing full traceability for regulatory audits while reducing documentation errors.
Table of Contents
Toggle1. Industry Context & Customer Profile
Industry Segment: Pharmaceutical Manufacturing
The pharmaceutical manufacturing industry in Vietnam has experienced significant growth in recent years, with local companies expanding production capacities and multinational corporations establishing regional manufacturing hubs. This growth has brought increased scrutiny from regulatory authorities, both domestic and international, particularly regarding documentation practices and compliance with Good Manufacturing Practices (GMP).
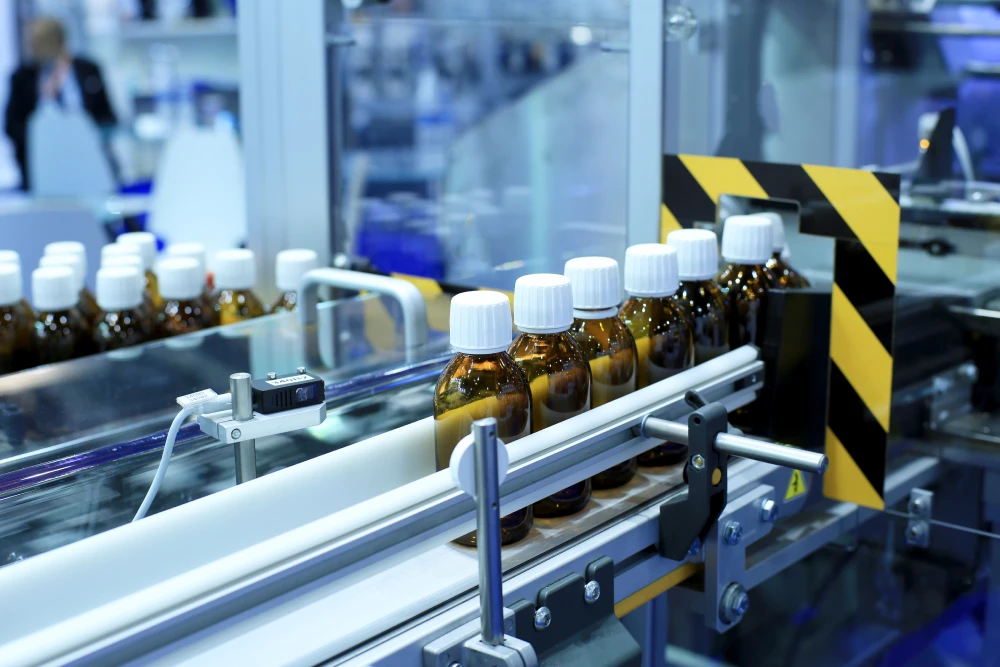
Typical Customer
Medium to large pharmaceutical manufacturers producing prescription medications, over-the-counter products, or active pharmaceutical ingredients (APIs). These companies typically employ 100-500 staff, operate multiple production lines, and manage hundreds of product variations with strict regulatory requirements for each.
Current Operational Environment
Most pharmaceutical manufacturers in Vietnam still rely heavily on paper-based batch record systems. This traditional approach involves:
- Printed batch production records with dozens to hundreds of pages per batch
- Manual documentation of each production step, parameter, and quality check
- Physical signatures for verification and approval processes
- Manual data transcription between production records and quality systems
- Paper storage of completed batch records in physical archives
- Time-consuming retrieval processes for regulatory inspections or investigations
This paper-based environment creates significant operational challenges while increasing compliance risks. One quality assurance manager at a mid-sized pharmaceutical company described their documentation process as “drowning in paper while hoping nothing falls through the cracks.”
2. Critical Pain Points & Challenges
Operational Inefficiencies
Paper-based batch record management creates substantial operational burdens:
- Production staff spend 25-30% of their time on documentation activities
- Batch release cycles average 2-3 weeks due to document review requirements
- Quality assurance teams dedicate 40-50% of their time to record review
- Document management requires dedicated personnel and physical storage space
- Information retrieval for process improvement is manual and time-consuming
These inefficiencies directly impact production capacity, time-to-market, and overall operational costs. As one operations director noted, “We have highly trained technical staff spending hours each day essentially doing clerical work instead of focusing on manufacturing excellence.”
Compliance & Quality Concerns
Paper-based batch records present significant compliance and quality risks:
- Documentation errors occur in approximately 5-10% of batch records
- Each error requires investigation, correction, and additional approvals
- Missing entries or signatures can delay batch release by days or weeks
- Data integrity issues are difficult to prevent without systemic controls
- Regulatory findings related to documentation are among the most common citations
- Cross-referencing related records for investigations is labor-intensive
For pharmaceutical manufacturers exporting to regulated markets like the US, EU, or Japan, these documentation challenges can threaten market access. Recent FDA inspections in Vietnam have increasingly focused on data integrity and complete batch documentation.
Cost Pressures
The financial impact of paper-based batch record systems extends throughout operations:
- Each batch record error costs an estimated $1,000-$2,500 in investigation time
- Delayed batch releases tie up millions in inventory value
- Document storage requires physical space costing $15,000-$30,000 annually
- Document retrieval for audits requires temporary staff augmentation
- Manual data entry prevents real-time analysis for cost reduction opportunities
Competitive Disadvantages
Manufacturers maintaining paper-based systems face growing competitive disadvantages:
- Longer time-to-market compared to digitally transformed competitors
- Higher compliance risks threatening access to regulated markets
- Difficulty implementing continuous improvement initiatives due to limited data access
- Higher manufacturing costs reducing profit margins
- Challenges attracting talent accustomed to modern digital work environments
3. DxFactory Solution Overview
Primary DxFactory Components
The DxFactory Electronic Batch Record (EBR) solution integrates two complementary systems:
- Enterprise Resource Planning (ERP) – Manages master data, material requirements, and production planning
- Quality Management System (QMS) – Handles batch record execution, review, and compliance documentation
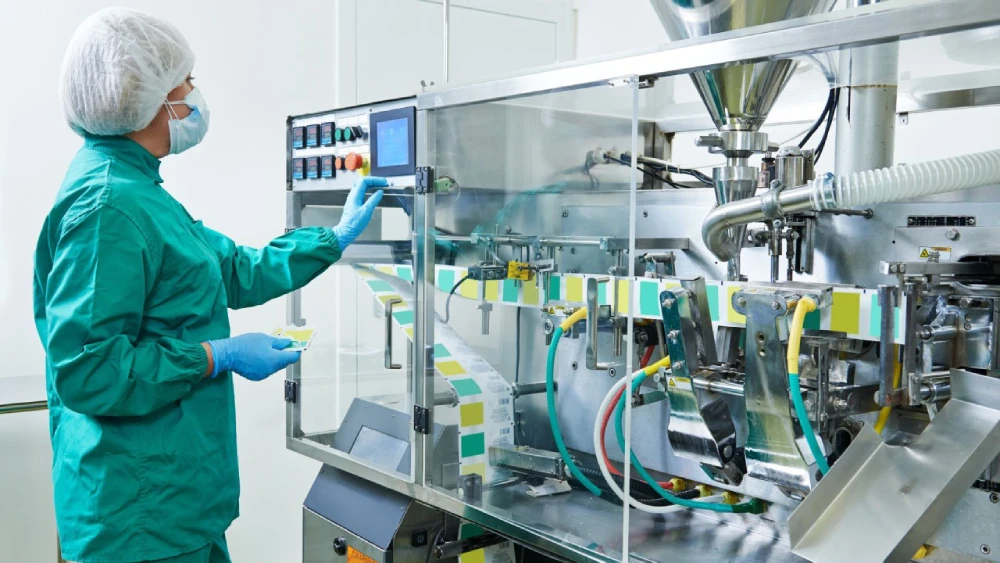
Key Functionalities
The integrated EBR solution provides comprehensive batch record management:
- Digital Workflow Management – Electronic execution and verification of each production step
- Exception Management – Real-time flagging and resolution of deviations
- Electronic Signatures – 21 CFR Part 11 compliant approvals and authorizations
- Automated Calculations – Error-free computation of yields, reconciliations, and other values
- Right-First-Time Manufacturing – Prevention of procedural errors through enforced workflows
- Audit Trail – Complete history of all actions and changes
- Automated Reporting – One-click generation of batch records and regulatory submissions
- Data Analytics – Real-time production monitoring and historical trend analysis
Integration Approach
The DxFactory EBR solution provides multiple integration capabilities:
- Connection with laboratory information management systems (LIMS)
- Integration with equipment and automated systems
- Data exchange with document management systems
- Compatibility with regulatory submission platforms
- Mobile device support for shop floor data entry
Technical Requirements
Implementation requires:
- Server infrastructure (on-premises or validated cloud)
- Network connectivity in production areas
- Workstations or tablets for production floor data entry
- Integration with existing manufacturing equipment where applicable
- Backup and disaster recovery systems meeting regulatory requirements
4. Implementation Roadmap
Phase 1: Assessment & Planning (4-6 weeks)
- Evaluation of current batch record processes and documentation
- Mapping of approval workflows and verification points
- Regulatory assessment and validation planning
- Risk assessment and mitigation strategy development
- Master data preparation and standardization
- Design of electronic forms and workflow templates
Phase 2: Deployment & Configuration (8-12 weeks)
- Installation and configuration of ERP and QMS systems
- Development of electronic batch record templates
- Setup of approval workflows and business rules
- Integration with laboratory and production systems
- Implementation of data migration strategy
- Configuration of reporting and analytics
Phase 3: Training & Adoption (4-6 weeks)
- Validation of system according to GAMP 5 methodology
- Development of standard operating procedures
- Training of production and quality personnel
- Parallel operation with existing paper systems
- User acceptance testing and feedback incorporation
- Regulatory documentation preparation
Phase 4: Optimization & Expansion (Ongoing)
- Performance monitoring and system refinement
- Addition of advanced analytics capabilities
- Expansion to additional product lines or sites
- Implementation of continuous improvement initiatives
- Regulatory inspection readiness maintenance
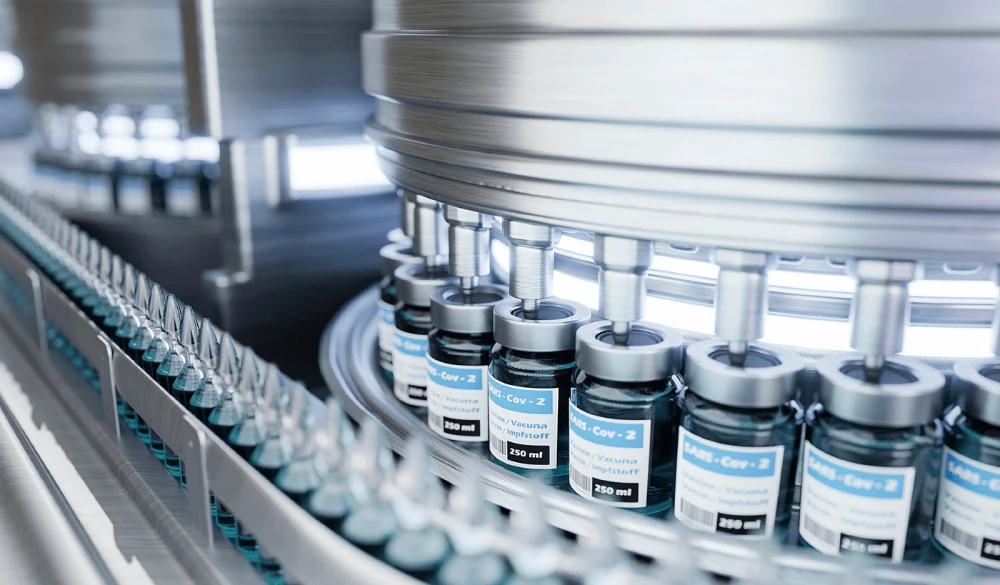
5. Value Delivery & ROI Analysis
Immediate Benefits
Within the first three months of implementation, manufacturers typically experience:
- 75% reduction in batch record errors
- 50% decrease in batch review time
- 100% traceability of all production activities
- 30% reduction in documentation time for production staff
- Elimination of missing data or signatures
Operational Improvements
Measured improvements after 6-12 months include:
- Batch release cycle time reduced from weeks to days
- Quality assurance efficiency improved by 40-60%
- Production output increased by 10-15% through reduced documentation time
- Deviation investigations completed 50% faster through better data access
- First-time quality rates improved by 5-10%
Financial Impact
A typical medium-sized pharmaceutical manufacturer can expect:
- Return on investment within 12-18 months
- Labor cost savings of $100,000-$200,000 annually
- Inventory holding cost reduction of $250,000-$500,000 through faster batch release
- Document storage cost elimination of $15,000-$30,000 annually
- Reduced risk of costly regulatory actions and market access restrictions
Competitive Advantage
Manufacturers implementing the DxFactory EBR solution gain significant competitive advantages:
- Faster time-to-market for new products
- Enhanced ability to meet regulatory requirements for global markets
- Improved agility to respond to market demands
- Data-driven decision making for continuous improvement
- Attractive, modern work environment for talent retention and recruitment
The transformation from paper-based to electronic batch records represents more than a technological upgrade—it fundamentally changes how pharmaceutical manufacturers approach quality, compliance, and operational excellence. As regulatory expectations continue to evolve globally, electronic batch record management has shifted from a competitive advantage to a business necessity. With the DxFactory EBR solution, pharmaceutical manufacturers can meet these challenges while simultaneously improving efficiency, reducing costs, and enhancing product quality.
Related Articles: